Introduction
In the field of robotics, control cables play a crucial role in ensuring efficient and accurate communication between the controller and the robotic system. These cables serve as the lifeline of robotic operations, transmitting signals and power to various components within the robot. As technology continues to advance, the demand for more sophisticated and reliable control cables has increased, driving innovation in the design and manufacturing of these critical components. In this comprehensive guide, we will delve into the importance of control cables in robotics, explore the key factors to consider when selecting control cables, and examine the latest advancements shaping the future of robotics control systems.
Importance of Control Cables in Robotics
Control cables are essential components in robotics systems, as they facilitate the transmission of signals and power between the controller and the various actuators, sensors, and other components of the robot. These cables are responsible for carrying commands from the controller to the different parts of the robot, enabling precise control over its movements and functions. Without reliable control cables, the performance of the robot would be compromised, leading to errors, malfunctions, and potential safety hazards.
In robotics applications, control cables are subjected to a wide range of environmental conditions, such as extreme temperatures, moisture, vibration, and mechanical stress. As such, it is crucial to select control cables that are designed to withstand these challenging conditions while maintaining optimal performance. The quality and reliability of control cables directly impact the overall efficiency, accuracy, and safety of robotic operations.
Key Factors to Consider When Selecting Control Cables for Robotics
When choosing control cables for robotics applications, several key factors must be taken into account to ensure optimal performance and reliability. These factors include:
1. Cable Type: There are various types of control cables available for robotics, each designed for specific applications and requirements. Common types of control cables include power cables, signal cables, and data cables. Power cables are used to transmit electrical power to the motors and other components of the robot, while signal cables carry control signals between the controller and the actuators. Data cables are utilized for transmitting data between different components of the robot, such as sensors and processors. It is essential to select the appropriate cable type based on the specific needs of the robotics system.
2. Cable Construction: The construction of the control cable plays a significant role in determining its performance and durability. Factors such as the conductor material, insulation material, shielding, and jacketing impact the cable's ability to withstand environmental conditions and mechanical stress. For example, cables with high-quality insulation and shielding provide better protection against electromagnetic interference (EMI) and ensure reliable signal transmission. The choice of conductor material also influences the cable's conductivity and flexibility, affecting its overall performance in robotics applications.
3. Flexibility and Bend Radius: In robotics systems, control cables are often required to bend and flex repeatedly to accommodate the movement of the robot's joints and actuators. It is essential to select control cables with a high degree of flexibility and a suitable bend radius to prevent damage or breakage during operation. Cables with a flexible construction and a small bend radius are better equipped to withstand constant movement and bending, ensuring long-term reliability in robotic applications.
4. Temperature Rating: Robotics systems may operate in environments with extreme temperatures, ranging from freezing cold to scorching heat. Control cables must be able to withstand these temperature variations without compromising their performance. Choosing cables with a temperature rating that matches the operating conditions of the robot is crucial to ensure reliable operation and prevent cable failures due to temperature extremes.
5. Mechanical Strength: Control cables in robotics applications are often subjected to mechanical stress, such as tension, torsion, and vibration. It is essential to select cables with a high level of mechanical strength and durability to withstand these forces without breaking or degrading. Cables with robust construction and high-quality materials are more resistant to mechanical stress, ensuring the longevity and reliability of the robotics system.
6. EMI/RFI Protection: Electromagnetic interference (EMI) and radio frequency interference (RFI) can disrupt the signals transmitted through control cables, leading to errors and malfunctions in the robotics system. To mitigate the effects of EMI/RFI, it is essential to choose cables with effective shielding and insulation. Shielded cables can block external interference and ensure clean signal transmission between the controller and the robot components, enhancing the overall performance and accuracy of the system.
7. Chemical Resistance: In certain robotics applications, control cables may be exposed to chemicals, oils, and other harsh substances that can degrade the cable's materials and affect its performance. Selecting cables with chemical-resistant insulation and jacketing materials is essential to protect the cables from damage and ensure reliable operation in challenging environments. Chemical-resistant cables are more durable and long-lasting, making them ideal for robotics applications where exposure to corrosive substances is a concern.
Advancements in Control Cable Technology for Robotics
The rapid evolution of robotics technology has driven innovations in control cable design and manufacturing, resulting in the development of advanced solutions that enhance the performance and reliability of robotic systems. Some of the key advancements in control cable technology for robotics include:
1. High-Flex Cables: High-flexibility control cables are specifically designed to withstand repeated bending and flexing in robotics applications. These cables feature a durable construction that allows them to bend without kinking or breaking, making them ideal for use in robots with articulated joints and moving parts. High-flex cables ensure reliable signal transmission and power delivery even in dynamic and demanding environments, improving the overall efficiency and longevity of the robotics system.
2. Hybrid Cables: Hybrid control cables combine power, signal, and data transmission capabilities in a single cable, simplifying the wiring and connectivity in robotics systems. These cables integrate multiple functions into a compact and lightweight design, reducing cable clutter and complexity in the robot's architecture. Hybrid cables enhance the efficiency and performance of robotics systems by streamlining the communication between the controller and the various components, leading to faster response times and improved overall functionality.
3. Shielded Cables: Shielded control cables are designed to protect against electromagnetic interference (EMI) and radio frequency interference (RFI) that can disrupt signal transmission in robotics applications. These cables feature a shielding layer that blocks external interference and ensures clean and reliable signal transmission between the controller and the robot components. Shielded cables are essential for maintaining signal integrity and accuracy in high-precision robotics systems, where any interference can lead to errors and malfunctions.
4. Ethernet Cables: Ethernet cables are increasingly being adopted in robotics applications for their high-speed data transmission capabilities and compatibility with modern control systems. Ethernet cables enable fast and reliable communication between the controller, sensors, and actuators in the robot, allowing for real-time monitoring and control of robotic operations. These cables support advanced networking protocols and protocols, making them ideal for robotics systems that require high-bandwidth data exchange and seamless integration with other devices and systems.
5. Armored Cables: Armored control cables are reinforced with a protective armor layer that enhances their durability and resistance to mechanical stress and external damage. These cables are suitable for robotics applications where the cables are exposed to harsh conditions, such as heavy machinery, sharp edges, or abrasive materials. Armored cables provide an extra layer of protection against physical impact and abrasion, ensuring the longevity and reliability of the control cable in challenging environments.
6. https://www.jiangyuancables.com/xlpe-insulated-sheathed-power-cable/ : Silicone control cables are known for their high-temperature resistance and flexibility, making them ideal for robotics applications that operate in extreme temperature environments. These cables can withstand temperatures ranging from -60°C to 200°C, ensuring reliable performance in both freezing cold and high-temperature conditions. Silicone cables are also resistant to moisture, chemicals, and UV radiation, making them suitable for outdoor and industrial robotics applications where exposure to harsh elements is a concern.
Future Trends in Control Cable Technology for Robotics
As the field of robotics continues to advance, the demand for innovative control cable solutions is expected to grow, driving the development of new technologies and materials that enhance the performance and reliability of robotic systems. Some of the future trends in control cable technology for robotics include:
1. Smart Cables: Smart control cables equipped with sensors and embedded electronics will enable real-time monitoring of cable health and performance in robotics systems. These cables can detect changes in temperature, vibration, and stress, providing early warning signals of potential cable failures. Smart cables will help prevent downtime and improve maintenance practices in robotics applications by enabling predictive maintenance and condition monitoring of critical cable components.
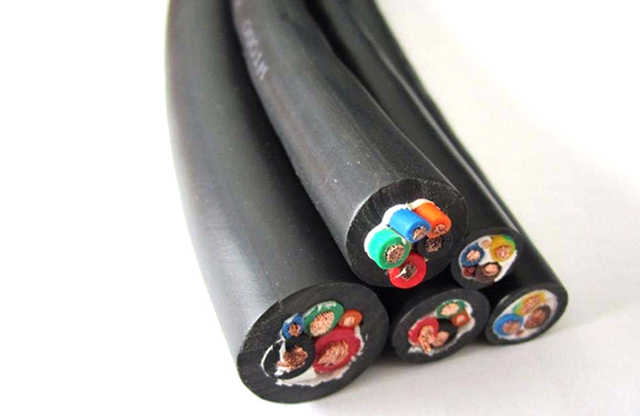
2. Fiber Optic Cables: Fiber optic control cables offer high-speed data transmission, immunity to electromagnetic interference, and long-distance communication capabilities, making them ideal for high-performance robotics applications. These cables provide reliable and secure communication between the controller and the robot components, enabling faster response times and improved system efficiency. Fiber optic cables will become increasingly popular in robotics systems that require high bandwidth, low latency, and high data security.
3. Wireless Cables: Wireless control cables utilizing technologies such as Bluetooth, Wi-Fi, and radio frequency (RF) will eliminate the need for physical cable connections in robotics systems, reducing cable clutter and simplifying the robot's architecture. Wireless cables enable flexible and seamless communication between the controller and the robot components, enhancing mobility and versatility in robotics applications. These cables will revolutionize the way robots are designed and operated, opening up new possibilities for collaborative and autonomous robotic systems.
4. Self-Healing Cables: Self-healing control cables with built-in repair mechanisms will automatically detect and repair cable damage caused by wear and tear, bending, or external factors. These cables can self-repair minor cuts, abrasions, or breaks, ensuring continuous operation and minimizing downtime in robotics applications. Self-healing cables will enhance the reliability and longevity of control cable systems in robots, reducing maintenance costs and improving overall system performance.
Conclusion
Control cables are essential components in robotics systems, enabling precise control, communication, and power transmission between the controller and the various components of the robot. Selecting the right control cables based on factors such as cable type, construction, flexibility, temperature rating, and mechanical strength is crucial to ensuring optimal performance and reliability in robotics applications. With advancements in control cable technology, such as high-flex cables, hybrid cables, shielded cables, Ethernet cables, armored cables, and silicone cables, robotics systems can achieve higher efficiency, accuracy, and durability.
Looking ahead, future trends in control cable technology for robotics, including smart cables, fiber optic cables, wireless cables, and self-healing cables, promise to revolutionize the way robots are designed, operated, and maintained. These innovative solutions will drive the next wave of advancements in robotics technology, enabling more intelligent, autonomous, and reliable robotic systems. By staying abreast of the latest developments in control cable technology, robotics engineers and designers can harness the power of advanced control cables to enhance the performance and capabilities of robotic systems across various industries and applications.